Pro Tips for Design of Shell-and-Tube Heat Exchangers
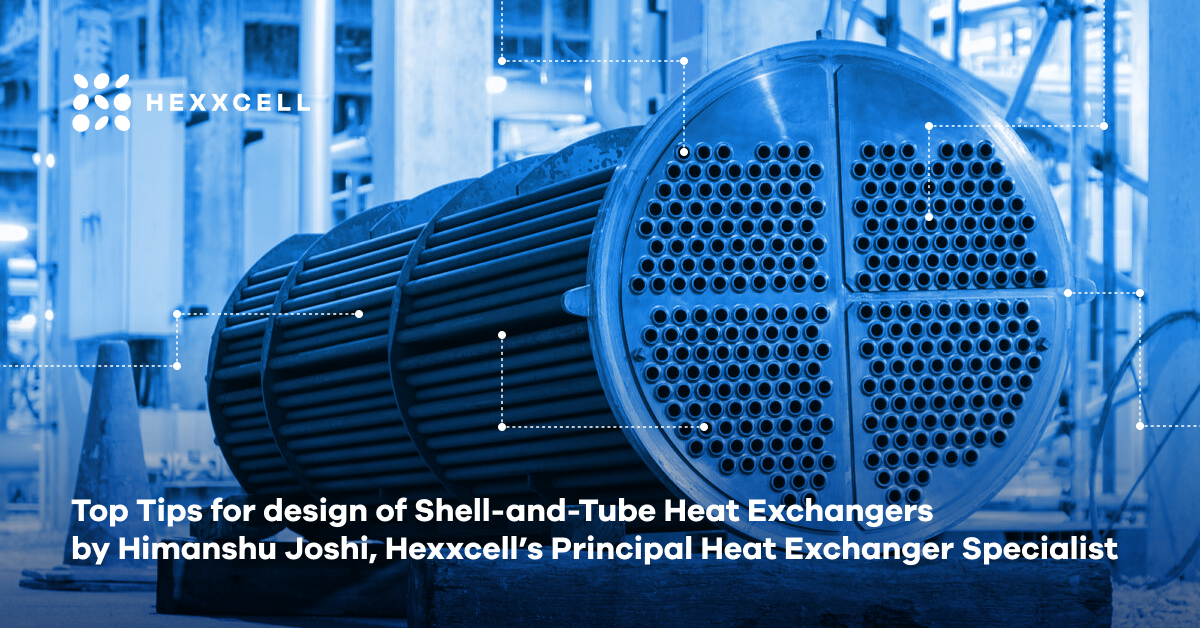
Heat Exchangers are ubiquitous in any process plant and their effective design is key to maximise energy recovery and minimise cost and environmental impact of operations. Follow these 11 pro tips to ensure a flowless design for your shell-and-tube heat exchanger:
1. Ask for as much pressure drop as necessary
In new projects, the process engineers may allocate available pressure drop per heat exchanger without recognizing that some cases may need more for a good design. In existing heat exchangers or for debottlenecking purposes the maximum pressure drop should be determined by what is already available. In both cases, the designer should make an estimate of what it will take to maintain good velocities or flow regimes and ask for that much pressure drop. Accepting what is first proposed and designing around it can often lead to a bad design. In debottleneck cases, consider what is actually available in the field rather than what was allowed in the original design.
2. Design for high velocities for single phase applications, especially liquids
High velocities lead to higher heat transfer coefficients and high shear stress which results in lower fouling when deposition of material is the major fouling mechanism. This is especially important in liquids - crude, FCC slurry, residues, heavy gasoils. High velocities come at the price of pressure drop (see Tip #1). A rough guideline is to have a minimum of 10 Pa shear stress to minimize fouling.
3. Avoid low velocity zones ("dead" zones) on the shell side, particularly important in single phase
Very low velocity or recirculating velocity zones are present at the locations where baffles meet the shell. These become ideal spots to deposit solids and build up fouling. Try to equalize the velocities in the window region and the crossflow between the baffle spaces to minimize the size of this dead zone.
4. Avoid wet-dry surface conditions in reboilers and steam generators
Fouling of reboilers (usually polymer deposition) and steam generators (scaling of salts) happens when the boiling surface is subject to conditions where vaporization leaves a solid deposit on the surface. This phenomenon is a result of the surface temperature being too high to sustain a liquid film, or the vapor traffic at the surface being too high such that liquid cannot fully wet the surface. Even if the average conditions look acceptable, always check whether this phenomenon can occur locally, for example where the wall temperature will be the highest or where liquid cannot reach the surface.
5. Avoid large unused surface on the shell cover side
Tube length which extends beyond the nozzle on the floating head or U-tube side iwasted surface area because there will not be sufficient flow over that surface. Since this is a low velocity area it also provides locations where fouling or scaling can occur. As much as possible put all the surface area where there is a reasonable amount of flow.
6. Check all designs for extreme conditions -- clean vs fouled, full flow vs turndown, start-of-run vs end-of-run.
A normal design will be done for typical process conditions (flows and temperatures), but extremes can result in problems. Clean conditions might have surface temperatures exceeding some problem-causing limit (cracking, scaling), especially in reboilers or cooling water heat exchangers. Turndown or bypassing for control purposes can result in high fouling due to low shear stress - for example, if a reboiler is oversurfaced and the hot fluid has to be pypassed. Bypassing cooling water for control purposes is usually detrimental from a fouling perspective. These situations are exacerbated if too much surface area margin has been provided (see Tips #2 and #11).
7. Ensure that thermophysical properties cover the proper temperature and pressure ranges
Sometimes the heat transfer and pressure drop calculations are very sensitive to variation in properties, especially viscosity, and viscosity at the tube wall temperature is a critical variable. Therefore, it is important that specified properties cover the wall temperature as well. The easiest way to achieve this is by providing a property grid from the hot inlet temperature to the cold inlet temperature for both fluids. If not specified correctly the design software may need to extrapolate, which may produce large errors for viscosity.
For reboilers and condensers it is important to cover the entire pressure range (inlet to outlet) and a temperature range which covers the vapor fraction range encountered in the heat exchanger.
8. Use fins when the heat transfer coefficient on one side is very low compared to the other side
Typical lowfin tubes provide a surface area enhancement of 2-3X, which can substantially reduce the size of the heat exchanger. Both OD and ID finned tubes are available, and are applicable in single phase as well as two phase flows. Fins can be used even if that side is expected to foul.
Contrary to the old belief, field operation has repeatedly shown that finned tubes foul at the same rate as plain tubes and are not more difficult to clean - especially with today's techniques like ultrasonic cleaning.
9. Check localized conditions for abnormal velocities, temperatures, vapor fractions etc.
Always look at parameters on a local basis instead of just the average for the whole heat exchanger. You may find zones of unacceptable velocities, temperatures, flow regimes etc. Try to fix these issues as much as possible. It is especially critical at the inlet and outlet spaces where the coldest or hottest temperature might create issues like film boiling or very cold wall temperatures - a problem which can be sometimes fixed by changing the direction of the shell side flow.
10. Ensure that mechanically needed devices such as impingement plates and support plates don't result in undesirable flow patterns
An impingement plate or support baffle (with or without a window cutout) can force the flow to take a path of least resistance thus bypassing heat transfer surface area. This can lead to underperformance even in a new heat exchanger. Use an arrangement of baffles and nozzle placement to force the flow to cover all the surface area. This can be important in single phase, condensing, and boiling.
11. Avoid providing excessive surface area margin
Allocating more surface area than necessary has two disadvantages - you get a larger, costlier, and heavier heat exchanger; and it can affect heat transfer as well as fouling. Reasonable margins (~10%) can be provided for process uncertainty or future increase in rates. However fouling margins provided via the use of a fouling factor are arbitrary and provide no protection in heat exchangers which foul heavily. And in clean services the fouling margin can make the heat exchanger larger by 50-100%.
.png)
About the author: Himanshu is an industry veteran with 34 years experience as a Heat Exchanger Specialist at ExxonMobil and Shell. He is now a Member of the Hexxcell's Scientific Advisory Board and our Principal Heat Exchanger Specialist. In his career, he has dealt with all aspects of heat exchangers from selection and design to operational troubleshooting and improvements.
He served as the Subject Matter Expert (SME) for fouling and heat transfer enhancement with both employers and conducted a fouling R&D program which has resulted in unique predictive methods.
He has published several scientific journal and conference papers and is a thought leader in the field of industrial and applied Heat Transfer.
If you'd like to get in touch with Himanshu, use our contact form: